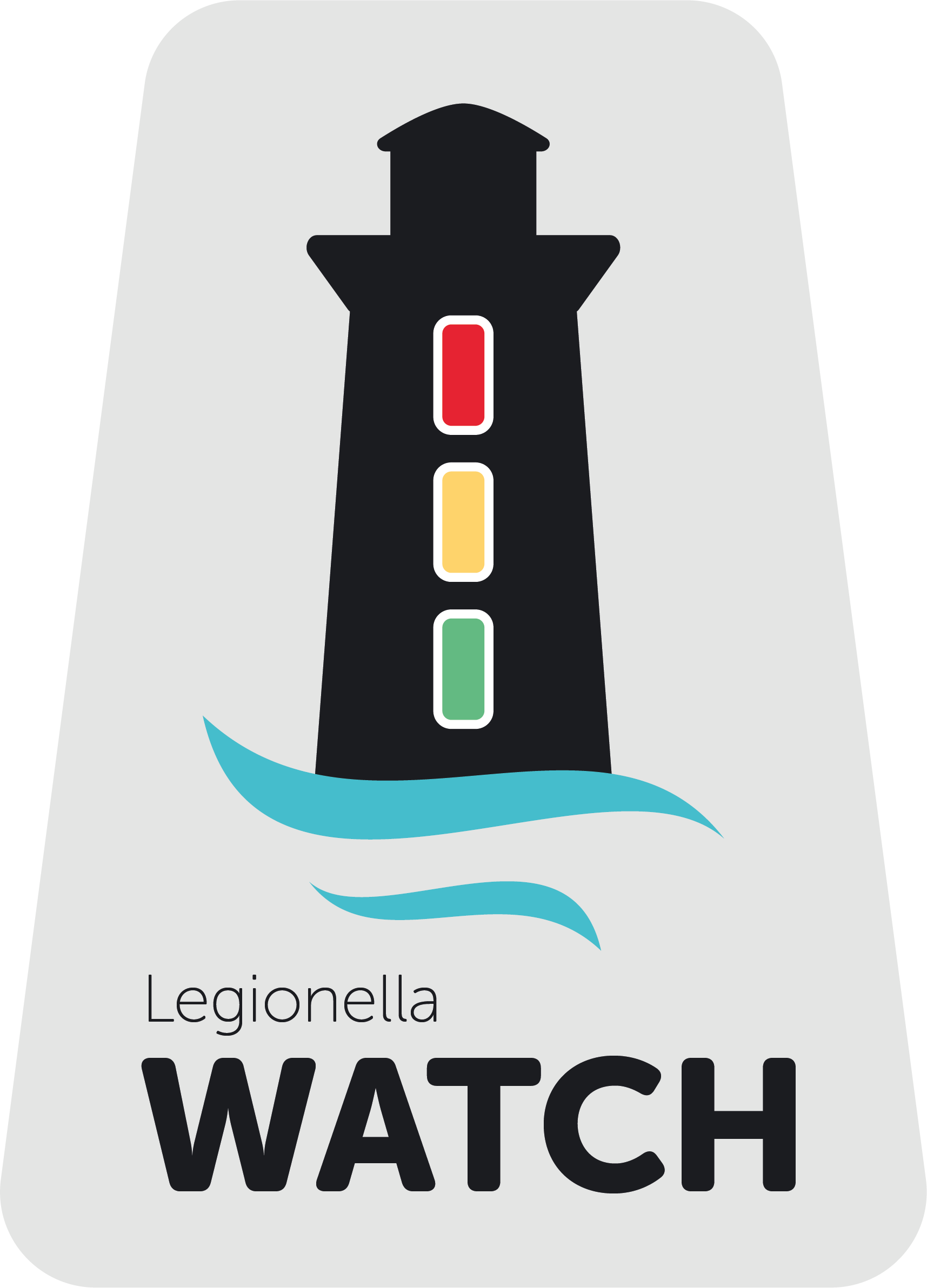
Legionella Information
This page is the place to go for all things Legionella! What is Legionella and Legionnaires Disease? How it is contracted by people and how to prevent this happening. Issues in the industry and best practices for Legionella control.
What is Legionella?
Legionella bacteria are widespread in natural water systems, e.g., rivers and ponds. However, the conditions are rarely right for people to catch legionnaires disease from these sources.
Outbreaks of the illness mainly occur from exposure to legionella growing in purpose-built systems where water temperatures stay high enough to encourage growth, e.g., cooling towers, evaporative condensers, and hot & cold water systems.
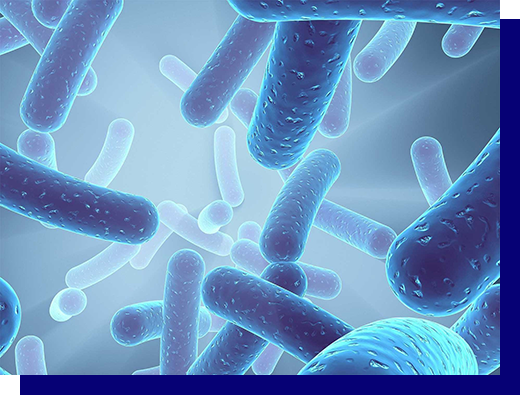
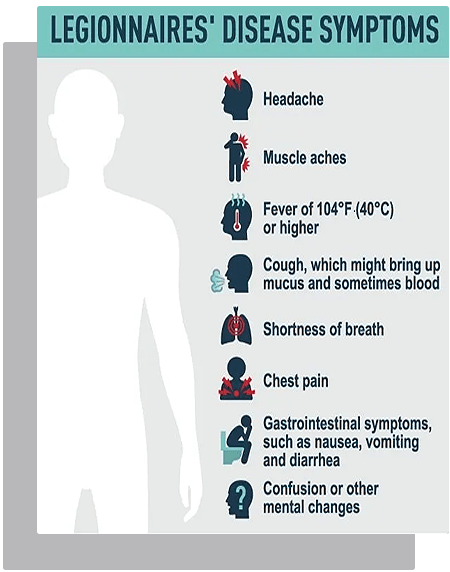
What is Legionnaires Disease?
Legionellosis is a collective term for diseases caused by legionella bacteria including the most serious Legionnaires' disease, as well as the similar but less serious conditions of Pontiac fever and Lochgoilhead fever. Legionnaires' disease is a potentially fatal form of pneumonia, and everyone is susceptible to infection. The risk increases with age, but some people are at higher risk including:
- People over 45 years of age
- Smokers and heavy drinkers
- People suffering from chronic respiratory or kidney disease
- Diabetes, lung, and heart disease
Anyone with an impaired immune system
How do you people get it?
People contract Legionnaires' disease by inhaling small droplets of water (aerosols), suspended in the air, containing the bacteria. Certain conditions increase the risk from legionella if:
- The water temperature in all or some parts of the system may be between 20-45 °C, which is suitable for growth.
- It is possible for breathable water droplets to be created and dispersed e.g., aerosol created by a cooling tower, or water outlets.
- Water is stored and/or re-circulated.
- There are deposits that can support bacterial growth providing a source of nutrients for the organism e.g., rust, sludge, scale, organic matter, and biofilms.
What is Legionella Monitoring?
Where the industry is right now!
There are 2 recognized methods of controlling legionella outbreaks in accordance with HSG274 Part 2 Temperature monitoring and chemical dosing.

Temperature Monitoring
Currently a manual process that involves monthly visits to a site by a trained engineer, to record the temperature of water at designated locations on the pipework known as sentinels.
This is fast becoming outdated as a way of monitoring temperatures for legionella control and there are good reasons for this. Site visits are not guaranteed due to the impact COVID still poses, nor is access to the required locations.
Temperatures are recorded on paper in most cases and there is no guarantee that the recorded temperatures are accurate. If one reading is not recorded, then another site visit is required sooner than normal.

Chemical Dosing
There are several different types of chemical dosing available that are considered effective in disinfecting water in accordance with HSG274 Part 2. Some of those are, Biocide treatments,
Chlorine dioxide and Copper or Silver Ionization. These treatments are very expensive to implement within existing water systems their running costs are not cheap either.
For this reason, they are mainly used by hospitals and large hospices.
See Video below for more information.
Automated Legionella Monitoring
A short video explaining the benefits of our Remote Monitoring Service - Legionella Watch
LAWS, LEGISLATION & RESPONSIBILITIES
Legal obligations apply to employers and to landlords – defined as anyone who rents out a home, or part of a home.
For landlords, Section 3(2) of the Health and Safety at Work Act 1974 sets out responsibilities to keep tenants safe from hazards. Landlords are included in the act’s definition of ‘self-employed’ people.
Duty holders are defined as employers, those in control of premises, and those with health and safety responsibilities for others.
The Control of Substances Hazardous to Health Regulations 2002 (COSHH) provides legal duties to control the risk from a range of hazardous substances, including biological agents (of which Legionella is one).
The relevant guidance is contained in the L8 Approved Code of Practice (ACOP) of 2001, revised and republished in November 2013. This is also known as ‘Legionnaires’ disease: The control of Legionella bacteria in water systems: ‘Approved Code of Practice’.
If risk assessments are undertaken for Legionella, then this should be done in accordance with HSG274 Part 2.
Testing or sampling for Legionella (sometimes referred to as microbiological monitoring) is not usually required for domestic hot and cold water systems, but only in very specific circumstances (HSG274 Part 2, para 2.120).
Testing for Legionella should not be confused with temperature monitoring, which is a reliable method for confirming the water system is under control.
Legionella Risk Assessment
It should be repeated whenever it is believed that there is a material change in any of the factors within the management plan, or any of the risk factors for Legionella. This will also include upgrades, or additions to the system.
- As a minimum, the hot and cold water system should be assessed for legionella risks every 2 years.
- it should also be repeated if there is any reason to believe that the organisation's duties are not being complied with, or the control measures are not adequate.
- A change of use of the building, change of system, or change in the responsible person all indicate the need for a new risk assessment.
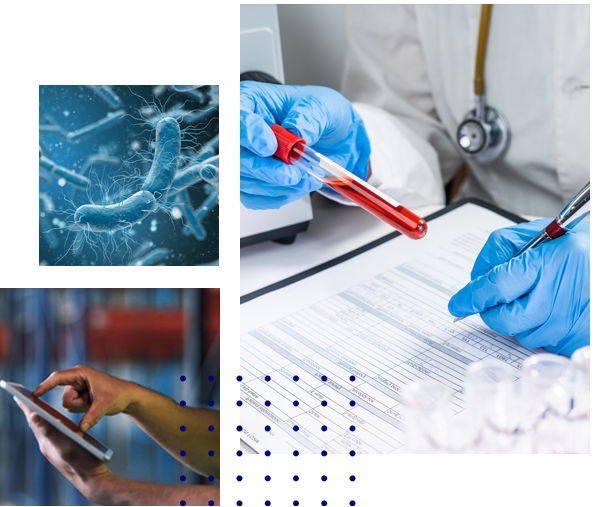
How to stay Compliant
- Assess the risk.
- Take care in cases where there has not been regular water usage and ‘turnover’. The water must not be allowed to stagnate. Either drain the system prior to being left for long periods or flush the system well if not used for a week or more.
- Ensure the hot water is at a suitable temperature (above 60 degrees Celsius) and moving through the system regularly.
- Ensure the cold water is at a suitable temperature (below 20 degrees Celsius) and moving through the system regularly.
- Avoid debris getting into the system (cold water tanks being a key risk for this).
- Minimises the need for water storage e.g., in tanks.
- Depending on the circumstances, there may be a need for specific control measures, such as automatic dosing of biocides or chemicals.
If you are an employer (with 5 or more employees) then you must keep a record of your Legionella risk assessment. If you are a landlord, there is no legal requirement to do so, but it is prudent, because it demonstrates that you have taken the suitable precautions that you are obliged to take.

The Problem with Manual
Temperature Monitoring
For years, the Legionella Monitoring Industry has worked with the man in a van approach.
A worker who visits sites and takes water temperatures manually
with a thermometer at specifically designated locations each month.
In the modern world we live in this is simply an out of date way of solving this problem.
New technology is enabling innovative methods to be introduced in the sector for the first time.
A site visit is planned for our worker to do his manual checks of water temperatures.
So many things can interrupt this site visit going ahead.
- The worker is unwell and cannot attend work
- The site has an unexpected issue and must close to all visitors
- The worker attends site but all keys are not available, so the visit is rearranged.
- The worker attends site but some keys are not available, so not all temperatures are recorded, and another visit must be arranged
- An asset on site is very difficult to get to and takes a long time to record the temperature each site visit
- HSG274 Part 2 states that a temperature reading must be recorded at least once a month
- This could in fact mean that almost 2 months is the period between some readings
- Temperature recorded on 1/4/2022 – April’s reading
- The next time a worker can visit site is the 31/5/2022 – May’s reading
- There has in fact been 60 days between reading taken however as a reading is recorded for April and May, this is deemed acceptable
- The worker is in a rush and enters readings without accurately taking the temperature.
There really are so many factors that can mean a temperature reading is missed or incorrect with the
current model of manual temperature recording that a more reliable method had to be possible.
Thankfully that time is here. By using a combination of innovative and smart technologies, remote temperature monitoring
is fast becoming the new industry standard. With data being constantly recorded by remote sensors and sent to
centralized visualisation platforms, the world of legionella compliance is firmly in the 21st century.
The world has changed!
The world has changed! This is not an opinion; it is a fact. Since Early 2020 when COVID-19 first hit the world, so many things have changed. Although we are now in a time of recovery and the restrictions on our lives do seem to have been lifted, many people are still working from home or ‘remotely’ as it is often referred to, many people are not going out as much as they did, many buildings have reduced staff numbers and many disruptions still occur in the aftermath.
- COVID-19 – Unfortunately, COVID-19 is still a big problem effecting so many aspects of life. The disruption of staff being off from work and the knock on effect of isolating is causing huge stress on the infrastructures in place across many industries.
- Access to sites and assets – With many organisations reducing staff numbers, accessing sites and assets within sites is becoming more difficult.
- Missed site visits – With many staff having to take unexpected time off from work, many planned visits for scheduled manual monitoring programs are not being carried out on time
- Missed critical readings being recorded – Many assets, especially those hard to reach are being missed from visits as there is no access available or no one to chaperon visiting engineers during planned site visits.
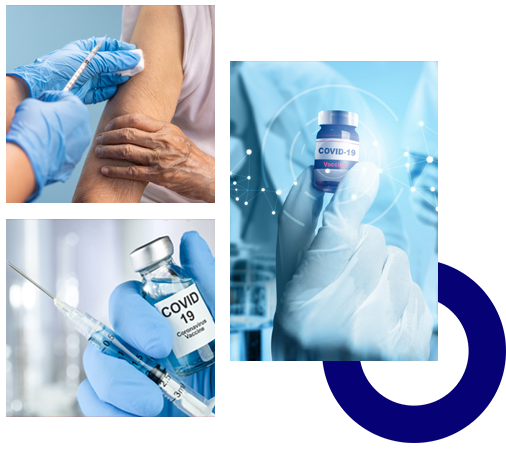
Remote IoT Sensors vs BMS
Remote IoT Sensors
This technology has opened the world of remote monitoring to everyone and everything. All sensors are designed to be retro fitted to assets, enabling them to be monitored in the same way a BMS systems does within more complex buildings and sites. With a fully modular approach, Remote IoT Sensors allows users to monitor their highest needing assets first and build their network up over time. Begin your journey with Legionella Watch and Remote Temperature Monitoring, simply keep adding new sensor types to expand your network, end your journey with an easy to manage, more compliant and Smart building.
BMS
Stands for Building Management Services or Systems. An approach used in large and complex buildings with a full complement of building services such as HVAC, Chilled and Hot Water and Heating, Lifts or elevators, Fire Alarms, Refrigeration, and Security Systems. All of these will be connected via a LAN (Local Area Network) to a Head End Terminal to be monitored by on site facilities staff. BMS systems are installed during a buildings construction and are very expensive to implement. They are normally focused on plant equipment with the further reaches of the system left unmonitored. The cost to extend a BMS to include these elements is often prohibitive, as the installation and commissioning of hard wired sensors after construction is completed can cause huge disruption.
Remote IoT sensors can be used to enhance existing BMS systems at a fraction of the cost. All sensors are plug and play and can be added to the network as and when they are required or desired. Grow your building environment data and see your building management optimisation in a new and smarter way!
Remote IoT Sensors vs BMS
Monitoring System

BMS
- Reduce Maintenance and repair costs.
- Provides a better working environment.
- Environment Friendly.
- Remote access means little or no down time.
- Security Risks
- Data Collection is difficult
- It is very expensive
- Installed during a building’s construction

Remote IoT Sensors
- Reduce Maintenance and repair costs.
- Provides a better working environment.
- Environment Friendly.
- Remote access means little or no down time.
- Data Collection is easy
- It is not expensive.
- Designed to be retro fitted.
- Makes tasks easier.
- Security Risks
What is Remote Monitoring?
Remote Monitoring is a general term for any remote sensor monitoring any type of asset. Normally battery powered and with wireless data transmissions, remote sensors are changing the world we live in. Sensors send data to IoT Network gateways, which then transmit it to hosted data servers connected to browser based software applications displaying the data on user dashboards. The ability to visualise data for so many aspects of building management gives huge control to the building managers. Precise decisions can be made, efficiency can be boosted, preventive maintenance can be adopted, and resources and finances can be saved.
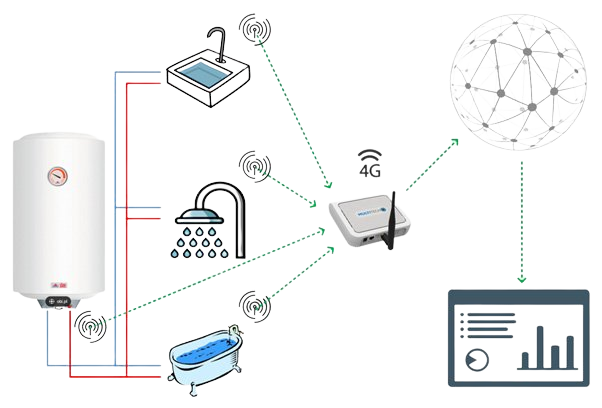
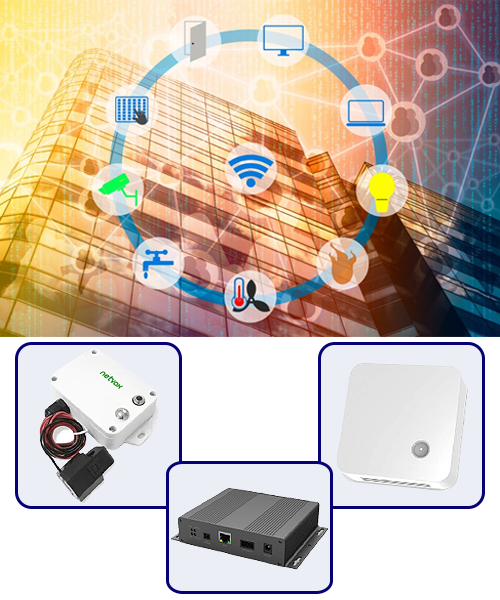
What is SMART Technology?
First, what does SMART mean? SMART stands for SELF-MONITORING, ANALYSIS and REPORTING TECHNOLOGY. It is a technology that uses artificial intelligence, machine learning, and big data analysis to provide cognitive awareness to objects that were in the past considered inanimate.
There are 3 main types of Smart Technology.
Internet of Things (IoT) - Describes the network of physical objects “things” that are embedded with sensors, chips, software, online connectivity, analytics, and applications to bring fixed physical objects to life. These devices create significant value, they are innovative, scalable, and automated.
Smart Connected Devices – Usually connected to the internet or Bluetooth and controlled remotely, smart connected devices can offer a tailored user experience but must be physically managed given that they don’t adapt to the extent IoT devices do. Smart Phones or Smart Bulbs are an example of Smart Connected Devices.
Smart Devices
- With reduced automation, no internet connection required, and of a programmable nature, smart devices, for instance, smart washing machines, provide specific personalized services at a particular time.
The whole process from installation to the updated weekly report has been fantastic.
Its purpose was to demonstrate how a newly installed system was operating for a 3-month period, so we could iron out any issues, or flag up any areas of concern before full hand over to the client. The real time data allowed us to make several minor adjustments and changes to achieve satisfactory temperatures throughout the property that would not normally be picked up.
Many Thanks for all your efforts, we shall definitely utilise this system on projects going forward